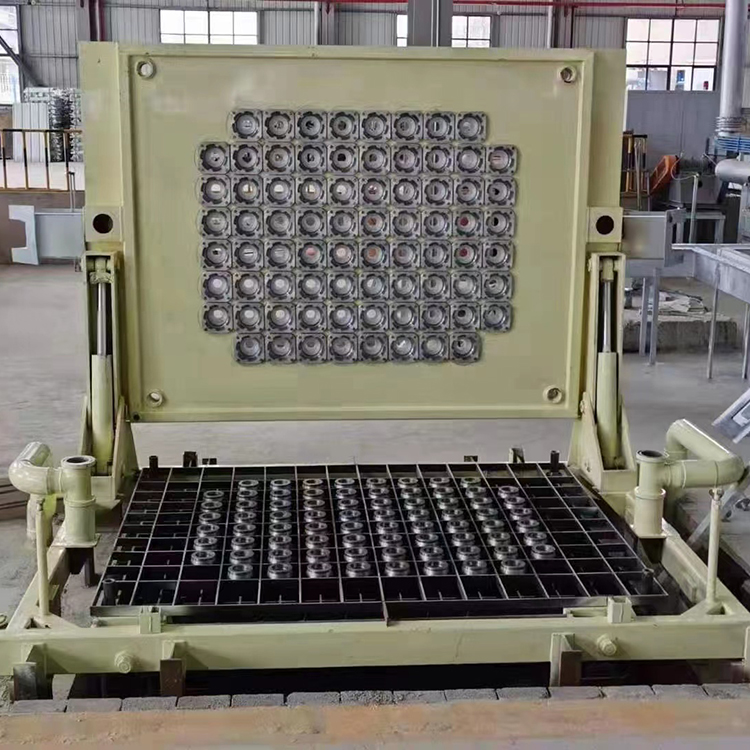
Founded in 1999, {Company} has established itself as a trusted manufacturer of high temperature refractory materials, including refractory bricks, aluminum silicate stopper cone, aluminum silicate wool boards, and more. With a focus on innovation and quality, the company has continuously invested in research and development to create products that can withstand the extreme conditions of metal melting and casting processes.
Oxidation is a common challenge in metal melting and casting plants, where high temperatures and chemical reactions can lead to the degradation of refractory materials. This can result in reduced efficiency, increased energy consumption, and costly downtime. To address this issue, {Company} has developed a range of refractory materials that are specifically designed to resist oxidation and maintain their integrity over extended periods of use.
One of the key solutions offered by {Company} is its advanced refractory bricks, which are manufactured using a special blend of materials that provide exceptional resistance to oxidation. These bricks are capable of withstanding the high temperatures and corrosive environments found in metal melting and casting plants, ensuring that the integrity of the refractory lining is maintained for prolonged periods.
In addition to refractory bricks, {Company} also offers aluminum silicate stopper cones that are utilized in the tapping and pouring of molten metal. These stopper cones are designed to withstand the erosive effects of molten metal and provide a reliable barrier against oxidation, ensuring that the quality of the cast metal is maintained throughout the production process.
Furthermore, {Company} produces aluminum silicate wool boards that are used as insulation materials in metal melting and casting plants. These boards are engineered to provide superior thermal insulation and resistance to oxidation, helping to optimize the efficiency of the plant and reduce energy consumption.
The development of these advanced solutions is a testament to {Company}'s commitment to delivering high-quality products that address the specific needs of the metal melting and casting industry. By focusing on the prevention of oxidation and the maintenance of refractory integrity, {Company} aims to help its customers improve their operational efficiency, reduce costs, and enhance the overall quality of their products.
In addition to its comprehensive range of refractory products, {Company} also provides technical support and consultation services to assist its customers in selecting the most suitable materials for their specific applications. With a team of experienced engineers and metallurgists, the company is able to offer tailored solutions that meet the unique requirements of each customer, ensuring optimal performance and longevity of the refractory materials.
As the demand for high-quality refractory materials continues to grow in the metal melting and casting industry, {Company} remains at the forefront of innovation, continuously developing new technologies and solutions to address the evolving needs of its customers. With a strong focus on quality, reliability, and customer satisfaction, the company is poised to make a significant impact in the global market for high temperature refractory materials.