Advantages of using instant silicon
The largest application field of magnesium is the addition of elements to aluminum alloys. The main purpose is to improve various performance indicators of aluminum alloy die castings, especially corrosion resistance. According to experts, aluminum-magnesium alloy die-casting is light and hard, has good corrosion resistance, is easy to weld and other surface treatments, and is an important material for manufacturing aircraft, rockets, speedboats, vehicles, etc. According to statistics, more than 45% of magnesium is used as an additive element for aluminum alloys in the United States every year, and magnesium is also used in a large amount as an additive element for aluminum alloys in China. In addition, magnesium is added to zinc die-cast alloys to increase its strength and improve dimensional stability. It is the lightest metal in practical use, and the specific gravity of magnesium is about 2/3 of that of aluminum and 1/4 of that of iron. It is the lightest metal among practical metals, with high strength and high rigidity. At present, the most widely used is magnesium-aluminum alloy, followed by magnesium-manganese alloy and magnesium-zinc-zirconium alloy. Magnesium alloys are widely used in portable equipment and automobile industries to achieve the purpose of lightweight. The melting point of magnesium alloy is lower than that of aluminum alloy, and the die-casting performance is good. The tensile strength of magnesium alloy castings is equivalent to that of aluminum alloy castings, generally up to 250MPA, and up to more than 600Mpa. The yield strength and elongation are not much different from those of aluminum alloys. Magnesium alloy also has good corrosion resistance, electromagnetic shielding performance, radiation protection performance, and can be 100% recycled. It is in line with the concept of green environmental protection and sustainable development.Product Dispaly
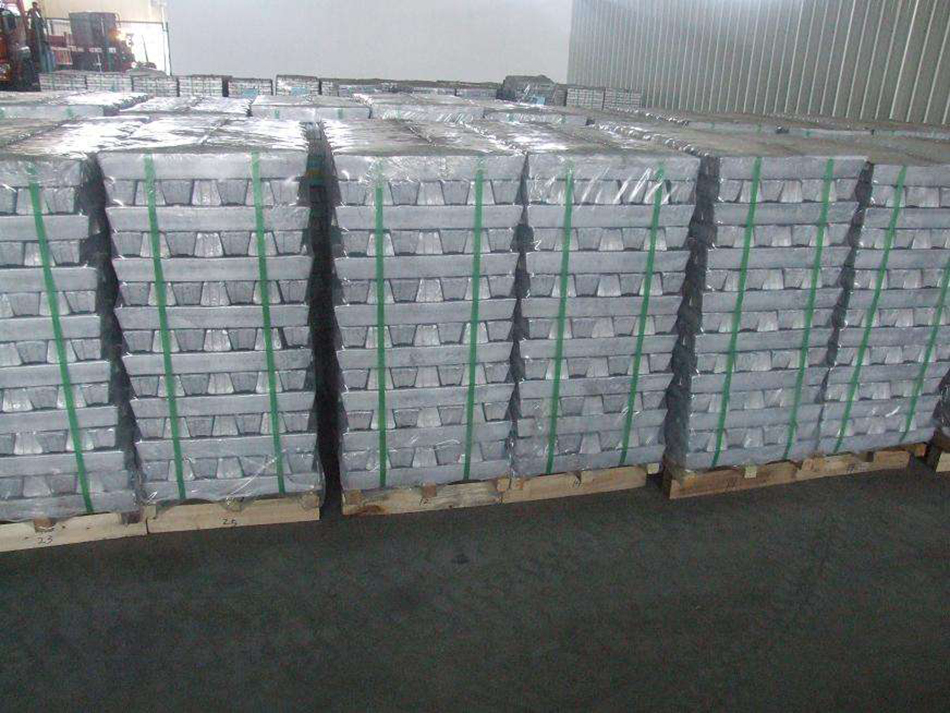
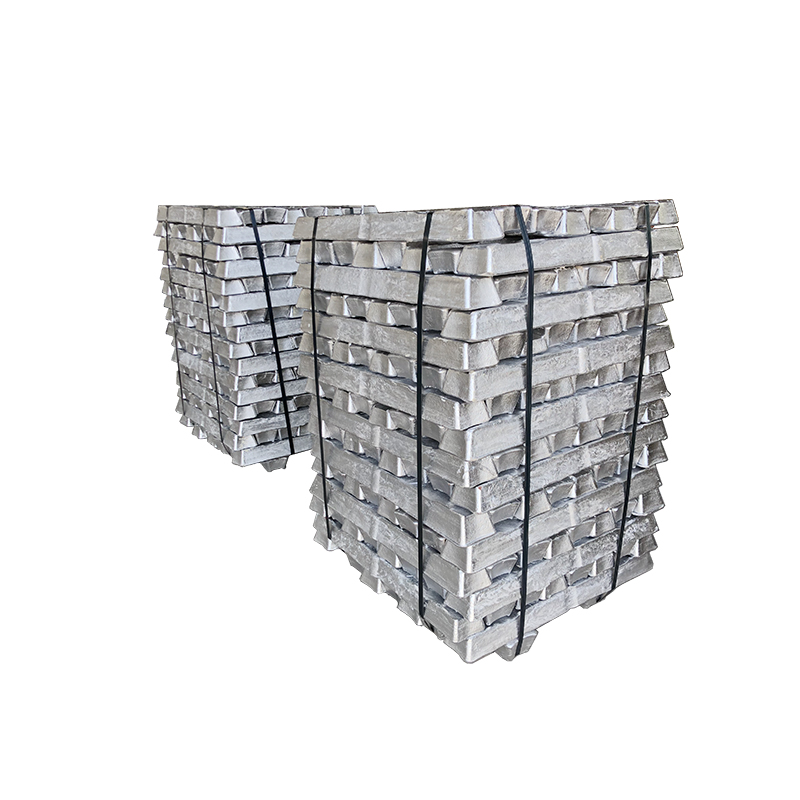